催化裂化裝置滑閥故障分析
由于其位置和作用特殊,用于催化裂化裝置上的單動、雙動滑閥工作時直接接觸高溫催化劑或煙氣,其正常運行與否直接關系到整個裝置的安全平穩(wěn)。通過對其工作原理及其典型事故進行剖析,提出了滑閥管理方法和預防事故發(fā)生的有效措施。
滑閥作為催化劑循環(huán)流程中的關鍵設備之一,在反應再生生產中,對催化裂化反應溫度控制、物料調節(jié)以及壓力控制起到關鍵作用。在緊急情況下,再生和待生滑閥還起到自保切斷兩器的安全作用。在同軸式催化裂化裝置中,滑閥也作為催化劑外循環(huán)的調節(jié)閥和安保切斷閥。此外,在催化裂化裝置的再生氣壓力控制中,煙氣流程上的雙動滑閥也同樣是起到兩器安全和煙機安全的保護作用。文中對滑閥生產運行中的典型故障情況進行了分析。
1、滑閥簡介
滑閥按照隔熱形式分為冷壁式和熱壁式。熱壁式是早期的技術,而冷壁式是20世紀90年代發(fā)展起來的,其應用更加具有代表性。
1.1、滑閥主要參數(shù)及結構
閥體材質為20g或16MnR,內壁采用100~150mm厚的耐磨隔熱雙層襯里,使閥體外壁工作溫度較低。對單動的再生、待生滑閥,其外表實測壁溫能夠控制在150~180℃。對雙動滑閥,閥體內操作溫度高達700℃時,其外壁溫度也不超過200℃。所以,冷壁滑閥的閥體材質大多采用16MnR低合金鋼,相對熱壁式滑閥,在材料應用和制造上降低了要求。
閥體與管道的連接采用同類材料焊接方式,現(xiàn)場組對焊接方便;y的出入口多采用等徑焊接結構,大蓋多采用圓形或矩形箱體結構。雙動滑閥則采用了類似單動滑閥的結構,只是對稱設置了2個箱體及大蓋。雙動滑閥的大蓋密封均采用了先進的唇型密封結構。冷壁單動滑閥閥體設計上主要采用等徑三通型焊接結構,雙動滑閥閥體采用異徑四通型焊接結構。催化裂化裝置中典型滑閥結構示意圖見圖1。
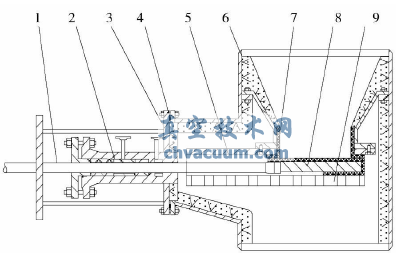
1.閥桿 2.填料函組件 3.閥大蓋 4.唇形密封 5.節(jié)流擋板組件 6.閥體 7.耐磨襯里 8.閥板 9.導軌
圖1 典型單動滑閥結構簡圖
1.2、滑閥內件構成
滑閥內件主要由節(jié)流錐、閥座圈、導軌及閥板等幾部分組成。
節(jié)流錐在滑閥內部,屬于高溫受力部件,承受著介質壓差及閥座圈、導軌、閥板的全部重量。節(jié)流錐為懸掛式,大端焊在閥體上,節(jié)流錐下部通過螺栓固定有閥座圈和導軌,閥板與導軌相對滑動,節(jié)流錐和閥座圈等可隨閥體內溫度變化而自由膨脹和收縮。
閥板和閥座圈形成滑閥的密封面。閥板密封面全部襯有耐磨襯里,并將閥板尾部隱蔽在密封面下面,蓋住閥桿頭部以增強閥板的耐沖蝕,并保護閥桿頭部不受催化劑的沖刷。閥座圈、閥板、導軌均為高溫合金鋼鑄造結構。
滑閥導軌采用L型截面,便于噴焊硬質合金和磨削加工。閥座圈的閥口四周和閥板頭部均襯有耐磨襯里,有效防止催化劑直接沖刷導軌與閥座圈的結合面,避免吹斷導軌螺栓。
閥板表面全部襯制龜甲網單層耐磨襯里。在催化劑沖刷嚴重的閥板前端和閥座圈的閥口處,均設有增強隔板來固定襯里。在閥板和導軌布置上,將導軌遠離閥口安裝,避免了催化劑直接沖刷導軌表面。閥板和閥座圈的重迭度增大,減少了通過間隙的催化劑通過量,減輕對導軌的磨損。
有數(shù)據顯示,國產冷壁單動滑閥導軌距離閥口為75mm,冷壁雙動滑閥導軌距離閥口為100mm,全關時的閥板頭部與閥口重疊大約50mm,有效地補償了閥板磨損,保障了全開閥門時的流道暢通。
1.3、滑閥密封部分結構組成
滑閥的閥蓋法蘭內表面襯有無龜甲網鋼纖維增強的單層襯里,閥蓋法蘭兩側和填料函上分別設有導軌和閥桿的吹掃接口,用于引進脫水蒸氣或其他氣體介質對滑閥導軌及閥桿進行吹掃、冷卻。
滑閥填料函采用串聯(lián)填料密封結構,見圖2。填料函內串聯(lián)裝入兩種不同材料和規(guī)格的填料,內側為備用填料,外側是工作填料。填料函操作時,備用填料松套在閥桿上并不壓緊,當工作填料失效或需要更換時,可通過填料函上備用填料處的注入口向內注入液體填料,將備用填料充實并壓緊,使該填料起到密封作用。在閥門正常工作、調節(jié)狀態(tài)下,也可方便地更換外側的工作填料。備用填料為浸油石墨盤根,工作填料為柔性石墨,液體填料可采用二硫化鉬鋰基脂或添加一定比例石墨粉進行配制。冷壁滑閥在安裝完畢后還應適當調整工作填料的壓緊量,以保證填料函的密封性能,調整原則是填料和閥桿之間的間隙不應過小,以免填料及閥桿過早磨損,功耗也會增大,嚴重時還會影響靈活性。
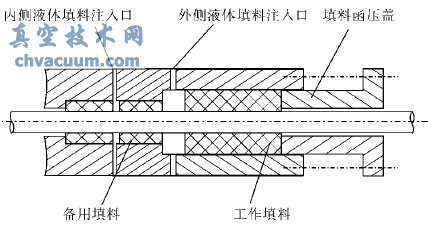
圖2 滑閥串聯(lián)填料密封結構示圖
1.4、控制技術
滑閥控制方式有電液控制、氣動控制和電機驅動控制模式。由于裝置現(xiàn)場安全要求和對控制精度要求越來越高,新建裝置上,滑閥控制方式則主要以電液控制為主流,小型的設備上依然還有氣動控制,但已經相對較少了。
滑閥電液執(zhí)行機構是由電氣控制系統(tǒng)、電液伺服閥、伺服油缸、油泵以及作為反饋元件的位移傳感器(或角度傳感器)等組成的典型電液伺服位置自動控制系統(tǒng)。電液執(zhí)行機構接受主控室4~20mA輸入信號,通過伺服放大器、電液伺服閥、高精度位移傳感器組成電液位置控制系統(tǒng),使伺服油缸活塞桿按指令信號作直線位移,通過機械連桿傳動,實現(xiàn)輸入信號和被控制設備的線性位移關系。
電液控制具有控制精度高、推力大、定位準確、響應快以及壽命長等顯著特點,電液執(zhí)行機構選用配件的隔爆要求都滿足國家強制標準,要求具有較高的安全等級。
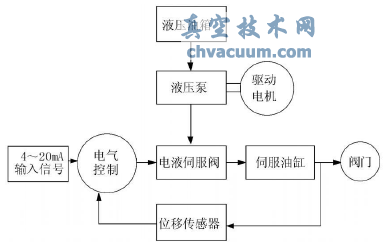
圖3 滑閥電液執(zhí)行機構原理示圖
2、滑閥的典型故障及對策
滑閥的故障大致可以分為滑閥本體故障和滑閥運行故障兩大類;y本體故障是指滑閥的本體導致的功能性故障、安全性故障。常見故障有閥道內耐磨襯里松脫、閥體內緊固件松脫、磨損、斷裂以及閥桿密封泄漏等滑閥的外部泄漏問題;y的運行故障主要指閥在生產運行中的控制部分故障。常見故障有滑閥的手動、自動切換機構卡阻,滑閥控制系統(tǒng)故障。
2.1、閥內件緊固螺栓斷裂及預防
2.1.1、閥內部螺栓斷裂
滑閥長期處于高溫狀態(tài)下,滑閥內部緊固螺栓的高溫蠕變疲勞斷裂是最為常見的內件故障問題。近幾年,國內煉化企業(yè)在生產過程中,出現(xiàn)滑閥內部螺栓斷裂情況多起,經過事故統(tǒng)計分析,閥內部螺栓斷裂是滑閥常見的設備本體故障。
滑閥設計中考慮到熱膨脹的綜合影響,所有內件均依靠導流錐懸掛,高溫下導流錐、閥座圈、導軌及閥板為主要的受力部件,它們承受介質壓差的全部重量。結構性的原因使內件之間的緊固螺栓在高溫下承受著巨大的拉伸力;y的內部緊固件為耐高溫合金螺栓,常用材料為高溫合金GH33,具有非常強的耐高溫煙氣腐蝕、抗H、N腐蝕的能力,同時也具有抗?jié)B碳腐蝕和S腐蝕的能力,具有很高的熱強性。由于長期持續(xù)在高溫下工作,螺栓經受周期性沖擊拉伸,螺栓的疲勞脆性斷裂傾向是明顯的。最常見的螺栓斷裂部位是滑閥導軌道與閥座圈的連接螺栓斷裂、閥座圈與導流錐之間的連接螺栓斷裂。
在生產過程中,內件螺栓的損壞表現(xiàn)為滑閥功能性故障。常見滑閥內件螺栓松脫和斷裂之后的現(xiàn)象:①閥板脫離正常的位置,在閥板與閥座圈形成的密封面就會出現(xiàn)泄漏空間,滑閥截流及切斷效果變差或者失效,泄漏形成的這個非正常通道就會成為流體介質的過流而加劇磨損。②閥板脫離正常位置,或者閥板與閥座圈一起脫離正常位置,閥桿頭承受來自于閥板的彎曲壓力,導致閥桿彎曲變形,使得滑閥開關出現(xiàn)卡澀,甚至卡死的故障。
2.1.2、采取措施
對于滑閥內件螺栓斷裂的應對措施,重點在故障預防和預防性檢修更換螺栓的工作上。該處螺栓一旦出現(xiàn)斷裂,不但會造成設備損壞,而且對生產造成重大影響,維修中去除斷在螺紋孔里的斷頭螺栓也是十分困難的。
按照滑閥使用企業(yè)的調研情況,以及對滑閥螺栓材料的理論分析表明,滑閥內部緊固螺栓在正常使用5~8a之后,推薦更換一次。如果使用中常有超過設計溫度的情況,其螺栓壽命應相應減短。鑒于當前國內石油化工企業(yè)在催化裂化裝置運行周期上多采用3a一修的管理周期。因此,建議對滑閥內部緊固螺栓采取2個生產周期進行一次全面更換是合適的,也是減免滑閥螺栓斷裂的重要手段。
2.2、大蓋密封泄漏及處理
2.2.1、大蓋密封泄漏
常見滑閥的大蓋密封有采用柔性石墨墊片密封和唇型密封兩類。由于高溫條件,實際應用中采用唇型密封的情況較多。唇型密封采用了緊固螺栓和密封焊接相結合的形式。唇型密封的連接螺栓緊固力應該均勻,最后的焊縫要均勻、連續(xù),避免砂眼等缺陷,以遏止最初可能出現(xiàn)的泄漏。緊固螺栓起到保持兩道密封面之間壓緊的作用。
現(xiàn)場多年的生產實踐表明,墊片密封泄漏往往會同時出現(xiàn)墊片損壞和法蘭面損壞。唇型密封泄漏的主要原因有兩點,其一是密封焊接中產生的氣孔、夾渣、砂眼以及裂紋等缺陷;其二是焊接金屬在煙氣介質和水蒸氣條件下形成腐蝕環(huán)境,由此導致焊縫穿透。
2.2.2、解決措施
(1)檢查消除唇型密封焊接缺陷
唇形密封在焊接過程中,容易形成穿透性氣孔、裂紋等缺陷,以致于無法起到隔離密封作用。這類問題在裝置開工期間的氣密試驗中能夠充分暴露,也易于處理。對于新的密封焊縫,焊逢金屬缺陷部位沒有明顯氧化層,韌性好,易于變形。針對該情況,可以采用鋼釬敲擊,鉚住漏點,然后進行動火補焊,或者撤掉滑閥的內部壓力再施焊。由于滑閥腔體內部有壓力,切忌直接補焊。
(2)唇型密封運行中的堵漏
對于生產運行中的唇型密封泄漏,由于泄漏部位介質外漏,在缺陷位置形成了氧化層,難以通過鉚接的辦法將泄漏點敲擊堵住。
實踐中,可以采用將漏點最近的兩邊密封面之間的間隙用焊肉填滿的方法。此處的焊接填充應避開緊固螺栓,防止螺栓受熱伸長、緊固力減弱引起新的泄漏。填充了焊接接頭與大蓋法蘭形成了對漏點的包圍,以進一步將漏點控制。
(3)運行中大蓋墊片密封泄漏的搶修
墊片密封泄漏問題很難處理。由于墊片的抗沖刷能力弱,泄漏擴張比較快,因而要求處理時間短。
生產實踐中,滑閥墊片泄漏的在線處理方案通常是沿法蘭邊沿包盒子,即沿法蘭邊沿一圈制作盒子,這樣才能將法蘭密封面完整地包起來。該方案能夠在保障堵住漏點的情況下,保護密封面在將來的可修復性。
2.3、閥桿密封泄漏處理
滑閥的閥桿在工作中相對于閥體都作往復運動。閥桿泄漏問題經常出現(xiàn)在長周期運行的后期或者檢修結束的初期。前者出現(xiàn)的原因是長周期運行中,閥桿的密封系統(tǒng)材料失效或者在使用中維護不當。后者主要為檢修施工質量差或者檢修選用配件質量差所致。常見的幾種閥桿故障情況及其處理方案如下。
(1)緊固填料壓蓋
閥蓋上的填料函采用串聯(lián)填料密封結構,1個填料函內串聯(lián)裝入了2種不同材料和規(guī)格的填料,內側為備用填料,外側是工作填料。正常操作時,備用填料松套在閥桿上并不壓緊,當出現(xiàn)泄漏跡象時,適當緊固工作填料壓蓋,即可消除泄漏。
(2)注入液體填料
對于串聯(lián)填料密封,工作填料完全壓緊即可實現(xiàn)密封。泄漏時,表明外側工作填料失效,需要啟用內側填料,并更換外側填料。通過填料函上備用填料處的注入口向內注入液體填料,將備用填料充實并壓緊,使該填料起到密封作用。在閥門正常工作、調節(jié)狀態(tài)下,也可方便地更換外側的工作填料。
備用填料為浸油石墨盤根,工作填料為柔性石墨,液體填料可采用二硫化鉬鋰基脂或添加一定比例石墨粉進行配制。液體填料通過專用工具從填料箱體上的專用注入口進入填料腔體里,擠壓內側備用填料,使其起到密封作用,隨著填料注入,閥桿泄漏會逐步減小,直到完全不漏。
(3)串聯(lián)填料密封更換
串聯(lián)填料密封有泄漏跡象時,首先緊填料壓蓋,通過進一步壓緊外側工作填料對泄漏進行封堵。當工作填料失效或需要更換時,注入液體填料,將備用填料充實并壓緊堵漏,使該填料起到密封作用。此時,閥門在正常工作狀態(tài)下,可方便地更換外側的工作填料。
在確認內側填料正常工作時,進行更換外側填料操作:①松開壓蓋螺栓,取下填料壓蓋。②按照安裝填料的逆向順序,用盤根鉤等工具依次掏出外側填料。③依據現(xiàn)場狀態(tài)判斷,在安全的前提下,盡可能掏盡外側填料。④清理外側填料箱內表面粘連的填料碎片。⑤把事先準備好的填料(盤根)按照技術要求依次裝填。⑥安裝填料壓蓋,按照技術要求緊固壓蓋螺栓,完成更換盤根工作。⑦注意調整工作填料的壓緊量,以保證填料函的密封性能和閥桿動作的靈活性,防止盤根與閥桿間隙過小,引起填料及閥桿過早磨損,也會增大功耗。
3、電液控制系統(tǒng)的常見故障及預防
滑閥的電液系統(tǒng)包括弱電、動力、過濾、壓控、電液轉換,液力放大和液力驅動等幾大部分,故障具有多樣性、復雜性、偶然性、必然性與隱蔽性等特點。
3.1、故障檢查
首先觀察故障現(xiàn)象,仔細了解故障產生的原因和故障產生前后設備的運轉狀況,查清故障是在什么條件下產生的,并摸清與故障有關的其他因素以及故障的特點等。一般可以采用目測、探聽、觸摸、鼻聞及儀器檢測等方法診斷查出故障部位。根據所核實的故障原因,先選擇經簡單檢查核實或修理即可使設備恢復正常工作狀態(tài)的項目,即采取先易后難的原則,排出檢查順序,以便在最短的時間內完成檢查工作。
液壓系統(tǒng)的主要問題常由于液壓油的品質問題或是電液控制閥的失效引起。電液控制閥故障的主要原因是液壓油的清潔問題。因此,液壓油的更換和管理是保障滑閥安全高精度運行的基礎條件。
3.2、電液系統(tǒng)的維護與保養(yǎng)
3.2.1、控制閥管理
控制閥作為電液系統(tǒng)組成部分,安裝在液壓泵和液壓缸之間,在系統(tǒng)中不作功,只對執(zhí)行元件起控制作用。液壓控制閥結構精密緊湊,其運行的可靠性主要與液壓系統(tǒng)設計選型和液壓油品質相關。
在日常運行維護中,應依據控制閥動作的頻繁程度設立不同的維護計劃。
(1)對于頻繁動作的控制閥,應定期更新。如對于伺服閥,應該依據實際情況定期更新,避免閥芯磨損帶來的負面影響。
(2)對于偶爾動作的控制閥,應依據生產實際,制訂計劃在線試驗其靈活性。如對于自保電磁閥,定期試驗既可以檢驗其可靠性,也可以使油流通過閥芯,沖刷長期靜止狀態(tài)下液壓油中沉積在閥芯上的雜質或變質物資,有利于疏通閥芯通道,避免閥芯卡澀。
(3)對于外彈簧式控制閥,應定期清洗。如對于滑閥油溫控制閥,外置的彈簧受環(huán)境影響,定期清理積灰和塵垢,能恢復其靈活性,保障使用效果。
3.2.2、液壓油管理
據資料顯示,70%~80%的液壓系統(tǒng)故障是與液壓油問題相關的。保障液壓油質量的穩(wěn)定及清潔度,有利于提高液壓系統(tǒng)的可靠性。
(1)滑閥油選擇
一般選用抗磨液壓油,油品粘度是液壓油的最重要使用性能指標之一。它的選擇合理與否,對液壓系統(tǒng)的運動平穩(wěn)性、工作可靠性與靈敏性、系統(tǒng)效率、功率損耗、氣蝕現(xiàn)象、溫升和磨損等都有顯著影響,甚至使系統(tǒng)不能工作。為此,選用液壓油時,要根據具體情況或系統(tǒng)要求選擇合適的粘度和適當?shù)囊簤河推贩N。
(2)油液清潔度
油液清潔程度是決定液壓系統(tǒng)能否正常工作的關鍵因素。據資料統(tǒng)計,液壓系統(tǒng)故障有75%是由于液壓油不清潔造成的。保持液壓油的清潔應采取有效措施:①防止外界雜質進入系統(tǒng)。按照技術規(guī)范要求制訂計劃清洗油箱,更新液壓油,并且一切添加液壓油的器具都必須保持潔凈,特別推薦購置滑閥用液壓油時選用小包裝型,避免添加過程中因分裝導致的二次污染。②液壓元件不要輕易拆卸,卸下的元件必須嚴格保持干凈,存放于無塵地點。清洗、檢查和裝拆液壓零件時,也應在無塵地點進行,總之,液壓系統(tǒng)零件一定要避免長時間裸露,以盡量減少雜質進入系統(tǒng)的機會。③過濾雜質防止系統(tǒng)產生污物。經常檢查過濾器差壓,檢查有無堵塞。防止油液變質產生沉積物,按要求定期清理油箱,清除沉積物并徹底換油。④定期檢查油質。檢驗液壓油的污染度和物化性能,其檢驗主要有兩個方面:一是油的物理和化學性能,如粘度、閃點、酸度、水分含量、抗泡沫試驗及防銹試驗等。二是檢查油中雜質顆粒大小和數(shù)量,即油的污染度。
(3)油溫
油溫主要影響油的粘度。油溫過低會使粘度增大使吸油困難。油溫過高會使粘度降低、油質變化、泄漏量增加、油液老化和變質,還會使密封件加速老化、變質和失效。油箱的油溫不能超過60℃,一般液壓設備的油量控制在35~60℃工作比較合適。
(4)保持足夠的油量
輸油量由執(zhí)行裝置的速度決定。為此,要求油箱的液面要盡量接近規(guī)定范圍的上限。特別是第1次運行時,當各液壓元件充滿油液后,一定要注意觀察油箱的液面高度,使液面接近允許液位的上限。
4、結語
隨著催化裂化技術的不斷進步和國內外催化裂化新技術、新設備的不斷應用,催化裂化裝置的規(guī)模也越來越大,滑閥直徑以及制造技術難度也由此增大;y位置關鍵,除了具有生產調節(jié)作用之外,也是裝置自保啟動情況下安全停車的關鍵設備之一,其安全運行性能將對整個裝置產生較大的影響。